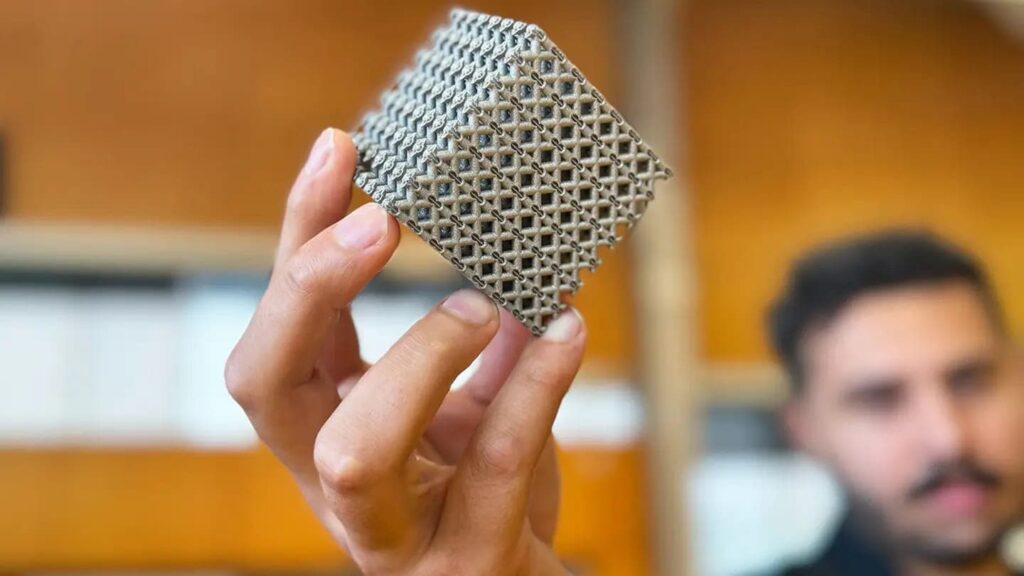
In the realm of engineering, the pursuit of innovation often hinges on overcoming longstanding challenges. One such hurdle has been the development of resilient lattice structures made from metal alloys, crucial for applications ranging from bone implants to rocket components. Despite years of effort, these “metamaterials” have struggled with uneven weight distribution, impeding their widespread adoption. However, a recent breakthrough by researchers at Australia’s RMIT University promises to revolutionize this field, drawing inspiration from nature and leveraging cutting-edge 3D-printing technology.
The study, published in Advanced Materials, unveils a novel approach to constructing lattice structures using a common titanium alloy. Engineers devised hollow struts with thin bands running through them, inspired by the resilience found in plants and coral. By integrating two complementary lattice structures, the team successfully mitigated stress concentration points, resulting in unprecedented strength and lightness—a feat previously unseen in synthetic materials.
Ma Qian, an RMIT Distinguished Professor of advanced manufacturing and co-author of the study, emphasized the significance of this breakthrough. In a university profile, Qian highlighted how the combination of innovative lattice designs addresses the inherent weaknesses in traditional metamaterials, paving the way for enhanced performance across various applications.
The manufacturing process behind these lattice metamaterials represents a convergence of advanced techniques, notably laser powder bed fusion. This cutting-edge method involves the precise deposition of titanium granules using a powerful laser beam, resulting in intricate lattice structures with unparalleled precision. Stress tests conducted on the newly developed lattice cubes demonstrated a remarkable 50-percent increase in weight-bearing capacity compared to conventional magnesium alloys used in aerospace engineering.
Despite already impressive performance metrics, the potential of these metamaterials extends further with the utilization of heat-resistant titanium alloys. With the ability to withstand temperatures up to 600 degrees Celsius, these materials hold promise for applications in rocketry manufacturing and firefighting drones, where extreme environmental conditions are commonplace.
Moreover, the hollow nature of these lattice structures opens doors for biomedical applications, particularly in the realm of bone implants. The porous architecture facilitates bone cell regrowth, promoting integration with the patient’s body—a critical aspect in enhancing the longevity and efficacy of medical implants.
While the transformative potential of 3D-printed titanium metamaterials is undeniable, challenges remain on the path to widespread adoption. Lead author Jordan Noronha, a PhD candidate at RMIT, acknowledges the current limitations in accessibility to advanced manufacturing technologies. However, Noronha remains optimistic, foreseeing a future where technological advancements and increased equipment availability democratize the utilization of metamaterial designs across industries.
In conclusion, the groundbreaking research conducted by RMIT University heralds a new era in materials engineering. By harnessing the power of 3D printing and drawing inspiration from nature’s resilience, researchers have unlocked the potential of titanium metamaterials to revolutionize diverse fields, from aerospace to biomedicine. As these innovations continue to evolve, they hold the promise of reshaping our technological landscape and pushing the boundaries of what is possible in engineering.